À Brognard, Meltblo France fabrique du meltblown, l’élément assurant le filtre dans les masques chirurgicaux, FFP2 et FFP3. La société, portée par Nicolas et Lucile Burny, est née de la crise sanitaire et participe à la relocalisation de ce composant essentiel à la production des masques. Nicolas Burny s’appuie sur 30 ans d’expérience dans le domaine.
À Brognard, Meltblo France fabrique du meltblown, l’élément assurant le filtre dans les masques chirurgicaux, FFP2 et FFP3. La société, portée par Nicolas et Lucile Burny, est née de la crise sanitaire et participe à la relocalisation de ce composant essentiel à la production des masques. Nicolas Burny s’appuie sur 30 ans d’expérience dans le domaine.
« Nous ne sommes pas des producteurs de masques », prévient, d’entrée, Nicolas Burny, président de Meltblo France, installé à Brognard, sur Technoland II. « Nous faisons le filtre présent dans le masque », complète-t-il en montrant un masque (photo ci-dessous) qu’il vient de découper pour présenter les différentes parties qui le composent, dont le filtre à l’intérieur. Et c’est ce filtre, le meltblown, qui sort depuis 6 mois de cet atelier de 1 400 m², qui tourne désormais 24 heures sur 24, 5 jours 7. « Le filtre, c’est la pièce stratégique du masque, souligne Lucile Burny, responsable de la communication. Sans filtre, pas de masque. » Le reste, c’est de l’habillage. « Et le filtre fait la différence entre un bon et un mauvais masque », appuie Nicolas Burny.
Mais avant de tomber le masque, justement, rembobinons. Premier trimestre 2020. Le monde plonge dans la crise sanitaire de la covid-19. La stupeur est générale. Au gré du déferlement de la première vague, les pays s’enferment à double tour. Mais on déplore une pénurie de masques à fournir aux soignants. Notamment. Sur les tarmacs, on joue des coudes pour récupérer les quelques cargaisons arrivées d’Asie, l’atelier du monde qui tourne au ralenti. Quand le couple constate ce déficit pour la fabrication des masques, il se dit que ce n’est pas possible qu’il ne fasse rien. Surtout que Nicolas Burny dispose d’un sacré savoir-faire dans le métier, une expérience de 30 ans, tant dans le spunbond, matière qui habille le masque, que le meltblown. Il a monté des lignes de production. A été directeur de production. Et depuis 2013, il est consultant dans le domaine. Au début de la crise, même le gouvernement le sollicite sur la question.
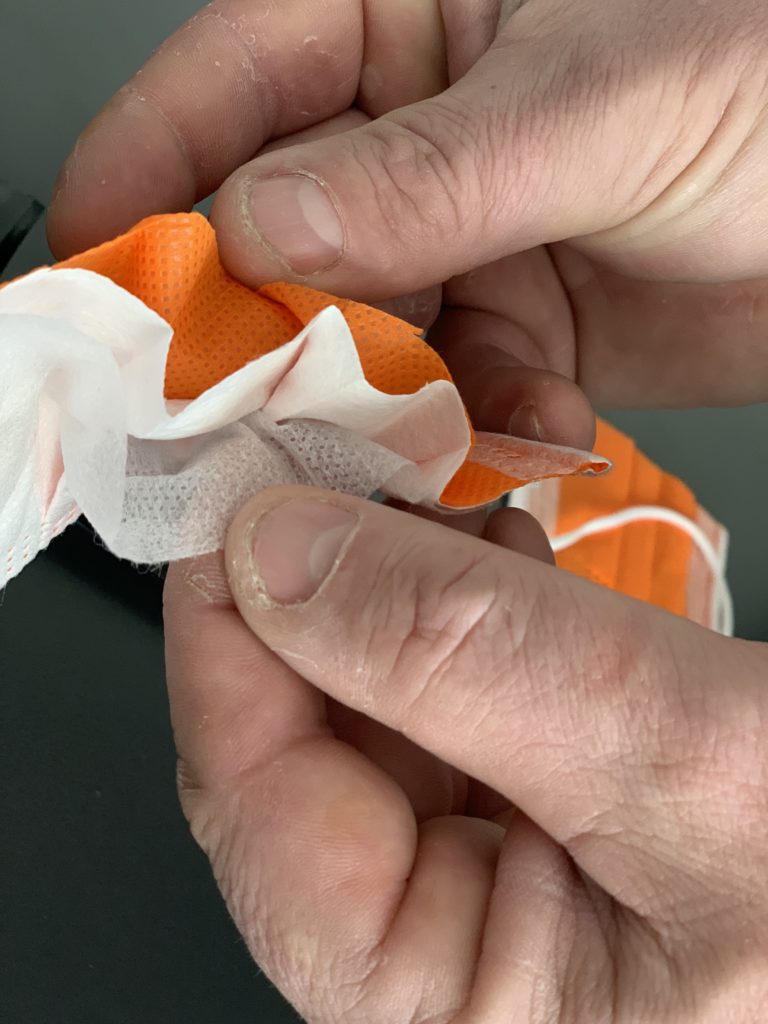
4 millions d’euros d’investissement
Le couple décide rapidement de se lancer dans l’aventure de la fabrication, en France, du meltblown, mais ne trouve pas de partenaires. Fin avril, l’État lance un appel à manifestation d’intérêt (AMI) pour la production de matériaux filtrants pour masques. Il y répond. Il est même parmi les 5 premiers dossiers sélectionnés. À côté, des entreprises de taille internationale qui enregistrent des chiffres d’affaires de plusieurs milliards d’euros ou de centaines de millions d’euros. Retenu par l’appel à projets, le dossier de Nicolas et Lucile Burny reçoit ensuite le soutien du conseil régional. Trois banques embraient également. Le couple investit aussi fortement ; il détient à 100 % la toute nouvelle société Meltblo France. Lucile et Nicolas ficellent alors un projet de 4 millions d’euros d’investissements. « On a bouclé cela en six mois », confie le couple, toujours impressionné.
Si le projet est lancé, maintenant, il faut répondre aux attentes. Le chantier pour les bâtiments débute à Brognard le 1er mars 2021. Fin avril, on installe les équipements. De mai à juillet, on développe et on valide les produits. La production a été lancée en juillet et suit un rythme industriel depuis septembre. « C’était un véritable marathon. Il fallait démarrer le site, mettre au point les produits et les produire », note Nicolas Burny. Le défi était immense, les risques considérables, mais ils l’ont relevé. Aujourd’hui, l’outil de production tourne à 100 %.
[ En images ]
Photos prises par Le Trois – Thibault Quartier
Filtration et respirabilité
Sur la ligne de production, les billes de polypropylène deviennent, au fil du process industriel, une longue toile non tissée qui s’apparente à un nuage ; c’est le meltblown. Il sera ensuite enroulé, pour être expédié chez des fabricants de masques. La qualité dépend du mélange des matières premières, du process industriel et du savoir-faire. Une vraie potion magique concoctée par une équipe de 12 personnes. Et ce produit monte en gamme lorsque l’on passe des normes des masques chirurgicaux à celles des masques FFP2, puis des FFP3. On accroit notamment les exigences de filtration. Pour les masques chirurgicaux, la norme demande que la filtration des bactéries d’une taille supérieure à 3 microns soit supérieure à 98 %. Pour les FFP2, l’exigence implique de ne pas laisser passer des bactéries supérieures à 0,3 micron, soit des bactéries dix fois plus petites. Par comparaison, le diamètre d’un cheveu oscille entre 50 et 100 microns. « Plus on monte en gamme, plus la mise au point et la réalisation sont difficiles », observe Lucile Burny. La fabrication du meltblown répond aussi à un fragile équilibre entre qualité de la filtration et respirabilité du masque.
Pour promouvoir la production française et sa qualité, le gouvernement a publié au mois de décembre un guide d’achat pour les organismes publics, qui les aide à définir les critères. Et dorénavant, le prix n’est plus le seul critère. On retrouve la qualité de filtration, la sécurité de l’approvisionnement, les délais, les conditions sociales de production, des critères environnementaux. La volonté est aussi « de maintenir la filière », estime Nicolas Burny. Qui complète : « Notre grande force, c’est la traçabilité du produit. » Tant sur les matières premières, que sur le jour de production du meltblown ou les conditions. « C’est très important et on ne l’a pas en Asie », souligne-t-il pour mieux marquer l’exigence de son produit.
Depuis le départ, l’entreprise a mis l’accent sur la R&D. Deux docteurs en chimie des polymères ont été embauchés. La volonté est de mettre l’accent sur la qualité du meltblown, mais aussi de prévoir de nouveaux débouchés pour ce composant filtrant, quand la demande en masques aura baissé ; on le voit bien avec la vague Omicron, la demande est extrêmement forte actuellement. « Il faut se projeter sur l’après covid-19 », sourit Lucile Burny. Des débouchés sont possibles dans plusieurs domaines, comme l’automobile ou les climatisations. « Le meltblown est un produit que l’on ne voit pas, mais que l’on retrouve partout », remarque Lucile Burny. Et à Brognard, on sait ce qui se cache derrière le masque.