2023 marque une année importante dans le déploiement de la filière hydrogène,dans le nord Franche-Comté. Le grand public pourra touché du doigt cette technologie et l’utiliser au quotidien. À partir du printemps, sept bus du réseau Optymo rouleront grâce à cette technologie. Ce seront des bus électriques, motorisés grâce à une pile à combustible, alimentée par de l’hydrogène.
Le chantier a débuté par la destruction du bâtiment Dekra. Ensuite, les équipes ont coulé les fondations. Les équipements, selon le calendrier initial, seront livrés en janvier 2023. Ce sont des conteneurs abritant un compresseur, les moyens de stockage basse (30 bars) et haute pression (450 bars) et l’électrolyseur, fournis par McPhy. En février et mars, une phase d’intégration et de tests sera lancée. Les bus seront aussi testés et les chauffeurs vont avoir une phase d’acclimatation. La régie des transports du Territoire de Belfort (RTTB), qui gère la flotte de bus Optymo, a un accès direct à la station.
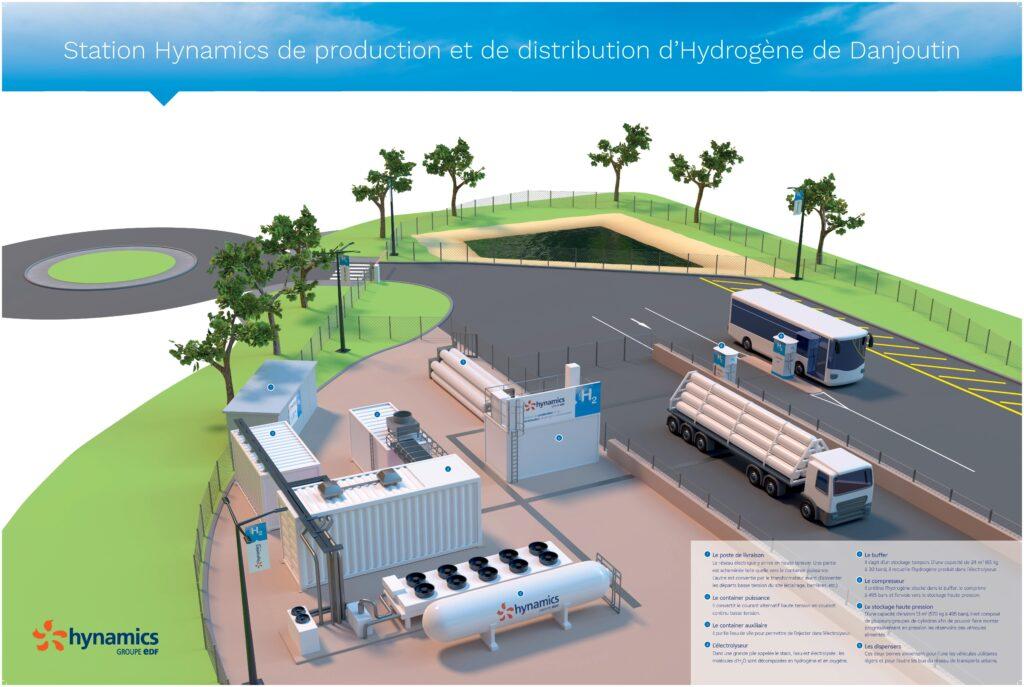
Multimodale
« La station a été pensée comme multimodale », rappelle Marie-Cécile Pardon, cheffe de projet de la station hydrogène de Danjoutin, chez Hynamics. La station pourrait remplir également des tube trailers, qui pourront fournir des clients en hydrogène dans la région. « C’est en discussion », convient la chef de projet, pour vendre les volumes supplémentaires.
Dans un premier temps, la station aura une capacité d’1 MW, capable de produire 400 kilos d’hydrogène par jour. Cette période doit permettre de s’acclimater à la technologie. On estime à 120 kilos le besoin quotidien des sept bus, en moyenne annuelle. En 2025, la station aura une capacité de 2 MW, pour alimenter les 27 bus de la flotte Optymo, qui sera renforcée. Le besoin sera de 520 kilos d’hydrogène par jour en moyenne annuelle.
Les 280 kilos d’hydrogène (30 % de la production) restant permettront de couvrir des applications autres que les bus. Cela ouvre des possibilités aux usages industriels, avec le remplissage de tube-trailers (remorque de tubes d’hydrogène comprimé),exportés, et à des transporteurs extérieurs, qui viendront se recharger. Et la station, modulaire, peut aussi être renforcée en termes de capacité, tout en sachant que l’option tube-trailers, qui offre des capacités d’export de l’hydrogène, octroie aussi une capacité d’import d’hydrogène, si les besoins sont plus importants que la production journalière de la station.
- Si vous souhaitez acquérir notre hors-série dédié à la filière hydrogène, écrivez à : redaction@letrois.info
L’atelier de la RTTB s’adapte à l’hydrogène
Qui dit nouvelle motorisation de bus, sous-entend nouvelles contraintes. Les ateliers étaient déjà adaptés à l’accueil des véhicules Atex (atmosphères explosives) GPL. Pour autant, les contraintes ne sont pas les mêmes avec les véhicules ATEX hydrogène. « Le GPL est un gaz lourd qui a tendance à stagner au sol, donc les détecteurs de gaz sont en bas, glisse Yannick Monnier, le directeur de la régie des transports du Territoire de Belfort (RTTB). L’hydrogène, c’est l’inverse. » Les capteurs sont installés au plafond. Avec l’hydrogène, ce que l’on surveille, c’est la concentration. Un système d’extraction a été installé sur le toit, capable de brasser 33 000 m3 d’air par heure, « soit le volume complet d’air du bâtiment renouvelé dix fois en une heure », détaille Yannick Monnier. En termes d’alerte, le système est très prévoyant. Dès que l’on atteint 10 % de la limite inférieure d’explosivité (LIE), les alarmes se déclenchent ; la LIE désigne la concentration minimale au-dessus de laquelle la substance peut être explosive. « L’alarme retentit, il y a une ouverture automatique des portes et les extracteurs se mettent en route pour extraire l’hydrogène, qui se disperse dans l’air », décrit le directeur, avant d’ajouter : « L’hydrogène n’est pas un polluant. » L’objectif est d’empêcher la formation d’une poche de gaz. Si on atteint le seuil de 20 % du LIE, on coupe en plus l’alimentation générale du site. Le sol est revêtu d’un revêtement antistatique, « relié à la terre », ajoute le directeur. Dans la zone Atex, il n’y a plus de tubes en plastique et les leds sont remplacées par du verre. Les mécaniciens auront une combinaison spéciale pour éviter l’électricité statique, lorsqu’ils interviendront sur la partie des réservoirs du bus, situés sur le toit du véhicule. Ils seront aussi équipés d’un explosimètre. Les véhicules sont enfin reliés à la terre avec des prises, dès qu’ils sont dans les ateliers. Par ailleurs, tous les salariés de la RTTB seront formés. 510 000 euros ont été investis pour adapter les ateliers et former le personnel. Si l’opération est concluante, l’achat de 20 nouveaux bus est programmé pour 2025.